Special Effects (SPFX)
Ngā Aratohu Ata Mariko
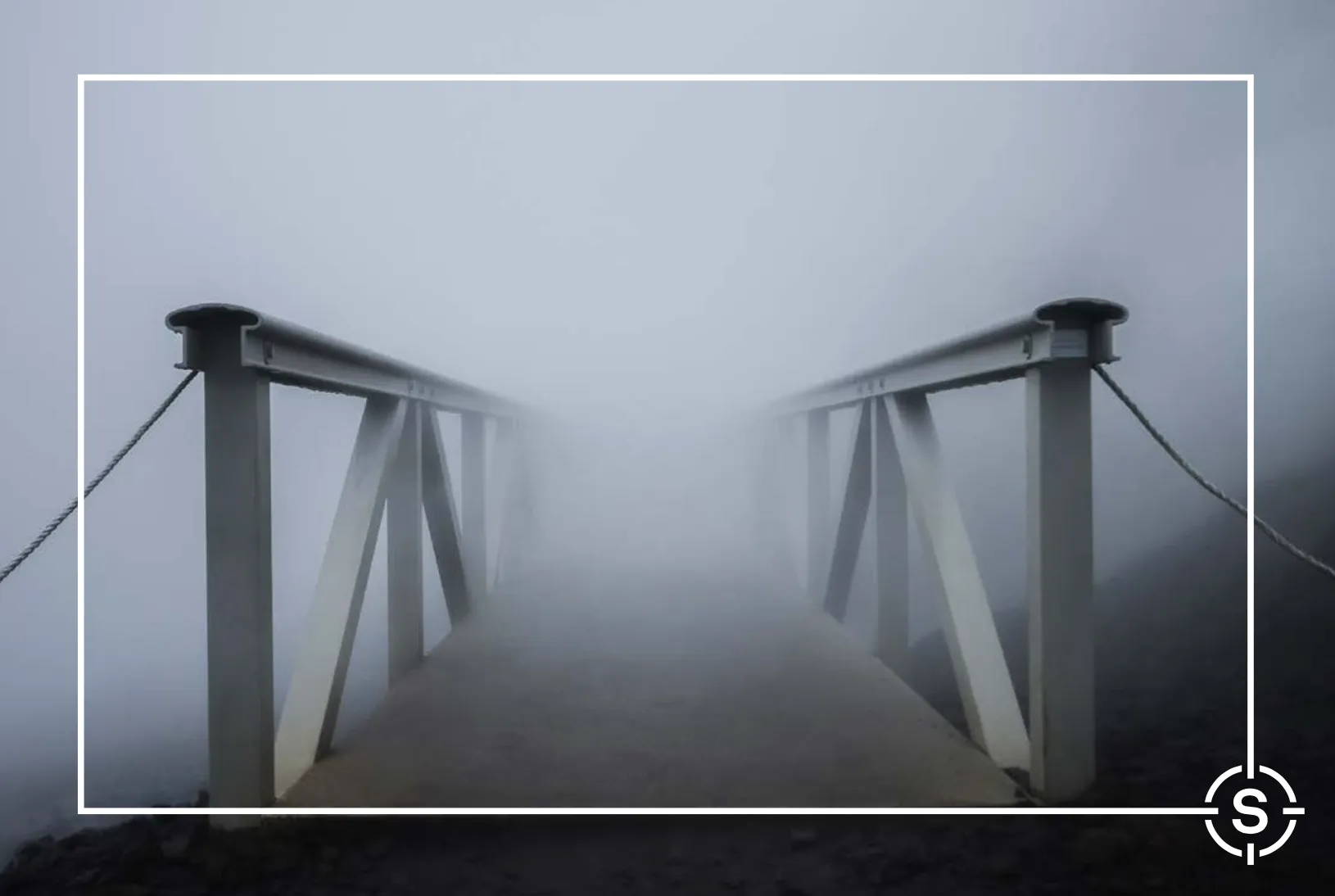
Special Effects
This chapter provides guidance in relation to working with special effects on a production.
The information provided within this chapter has been developed in consultation with special effects subject matter experts from within the New Zealand and international screen industry and draws from the Health and Safety at Work (Hazardous Substances) Regulations 2017.
Who needs to read this?
All workers who undertake work with, or work that interacts with, special effects should read and understand the section on ‘minimum responsibilities’ and ‘responsibilities specific to special effects’.
Roles that have specific responsibilities, or influence, over work with special effects should read the section on ‘planning and guidance considerations’ and ‘responsibilities specific to special effects’ – this includes producers, directors, production managers, line producers, heads of departments, assistant directors and health and safety officers.
Definitions
Atmospheric special effects are the use of artificial smoke and mists produced from chemicals or oil for theatrical purposes; this includes simulating steam, rain, wind, snow, water and wave effects.
Exclusions zones are areas defined by the person in charge / PCBU that may receive debris or malfunctioning pyrotechnics and help to ensure people’s safety.
Explosives may be high explosive, such as bullet hits, detonators, detonating cord, gelignite or TNT, or low explosive of the burning (deflagrating) or propulsive, such as flash or gun powder.
Hazardous substance means, unless expressly provided otherwise by regulations, any substance —
- with one or more of the following intrinsic properties – explosiveness, flammability, a capacity to oxidise, corrosiveness, toxicity (including chronic toxicity), ecotoxicity,
- with or without bioaccumulation; or which on contact with air or water (other than air or water where the temperature or pressure has been artificially increased or decreased) generates a substance with any one or more of the properties specified above.
Mechanical special effects are ways of creating special effects using, but not limited to, air mortar explosions, breakaways, falling objects, action props, flying sequences, counter weight systems, hydraulic, pneumatic and kinetic effects including the use of computer and hydraulic controlled Gimbals.
Open flames refers to the planned use of fire and combustible fuels for filming purposes.
Pyrotechnics are devices, compounds and mixtures that burn fiercely and produce light, heat, smoke or sparks in varying colours and quantities without an explosive effect.
Pyrotechnic special effects are ways of creating special effects using, but not limited to, explosives, pyrotechnics, fireworks, bullet hits and pyrotechnic smoke devices.
Note: that safety flares, parachute rocket flares and pyrotechnic smoke pots all fall into the category of pyrotechnics when used as special effects.
Special effects means the use of a physical mechanical and chemical process to produce on camera effects elements.
Special effects supervisor (SPFX supervisor) means the person responsible for the planning, preparation and use of special effects.
Special effects technician (SPFX technician) means a person responsible for the preparation and use of special effects under the supervision of a special effects supervisor.
Specific risks
- Chemicals and fumes
- Concussion from explosive blast overpressure
- Blunt force trauma from flying objects
- Lacerations from flying projectile debris
- Heat radiation from pyrotechnics, steam or fire
- Flash burns
- Loud noises
- Light flashes
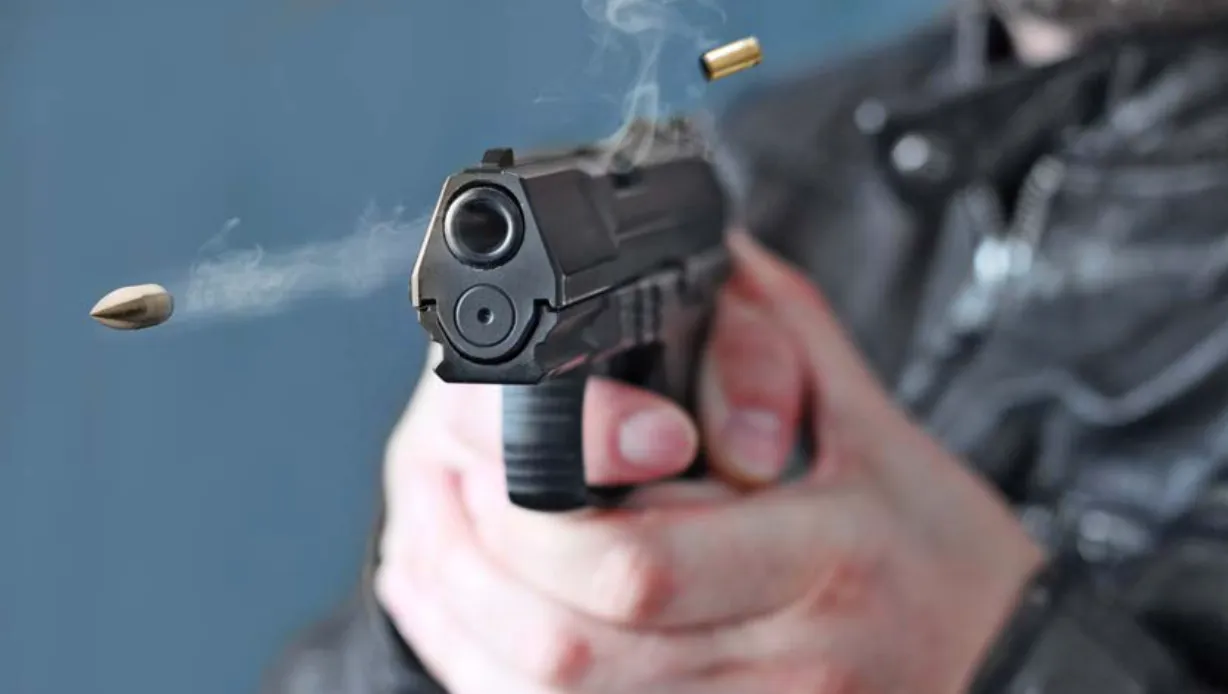
Minimum responsibilities
Everyone on a screen production who does, or could, work with special effects, should read and understand this section.
All workers:
- are required to follow all health and safety information, training and instruction they have received;
- must be aware of what personal protective equipment they are expected to provide themselves and what will be provided by the production;
- follow instructions provided by the person in charge of any activity that involves the use of, or is conducted near, special effects; and
- know escape routes, when working around or near special effects, and if they are unsure of the escape route check with the 1st assistant director to learn the escape route before entering the work area.
* All SPFX Supervisors and Technicians must also read the section on Responsibilities Specific to Special Effects.
Planning and Guidance Considerations and Responsibilities
Anyone who has specific responsibilities, or influence, over work with special effects should read and understand this section as well as the minimum responsibilities for everybody. This includes funders, Producers, Directors, Production Managers, Line Producers, Heads of Departments, Assistant Directors, SPFX Supervisors and Technicians, and Health and Safety Officers.
Further information about responsibilities related to special effects can be found in the following section.
While the production company is likely to be the primary PCBU (person in control of a business undertaking), all PCBUs (such as contractors) are responsible
for the overall safety of the workplace and those who are influenced by their work, including workers, visitors and other persons on, or in the vicinity, of that workplace.
Funders
Funders should:
- be assured, through the provision of the production’s health and safety plan, that the funding provided is adequate to provide for competent people, to undertake and supervise all work related to special effects, and the appropriate equipment required; and
- ensure that all senior contractors have sufficient insurance cover, appropriate to the risk and scale of the work to be undertaken.
Production Company
In pre-production, the production company must clearly identify who has control of special effects, and ensure those people are competent.
During production, production companies must consult, cooperate and coordinate with other PBCUs on set and subject matter experts, where necessary.
Producer and Production Manager
The Producer, Production Manager or person with delegated responsibility should:
- ensure all cast and crew are aware that explosives and pyrotechnics, open flame/ fire sequences or smoke producing equipment will be used
- ensure workers are aware of risks associated with special effects;
- ensure workers are provided appropriate personal protective equipment;
- consider how changing deadlines and making changes to briefs at the last minute can lead to fatigue and stress for workers;
- consider how changing work briefs, resulting in workers starting the project from scratch, can lead to stress for workers;
- consult and collaborate with the special effect supervisor to understand how long tasks will take and how deadlines may impact workload and final product;
- ensure hazard identification and risk assessments are undertaken for all applicable special effects;
- ensure all potential risks on location are eliminated or, if elimination is not reasonably practicable, minimised;
- ensure that emergency and first aid procedures are in place;
- ensure sufficient firefighting equipment is provided and that it is immediately available on set if required;
- ensure there is a clear access way for emergency and firefighting equipment and vehicles on set;
- ensure that all those who undertake specific effects hold the relevant permits/ licences;
- ensure that the SPFX Supervisor is allowed adequate on-set pre-production time unhindered by other filming or other crew or cast members;
- ensure that adequate testing of all special effects is carried out during pre- production and where possible that such testing is carried out in the presence of all relevant heads of department and those cast members involved; and
- ensure that the SPFX Supervisor always has in their possession all necessary permits and licences covering products and equipment used to carry out their contract of employment, together with literature on all relevant chemical compositions and safety guidelines regarding the use of pyrotechnics and flammable materials.
Assistant Director/s
The 1st Assistant Director will ensure that the SPFX Supervisor is allowed adequate on-set pre-production time unhindered by other filming or other crew or cast members.
In the absence of a Health and Safety Officer, the Assistant Director/s should:
- ensure hazard identification and risk assessments are undertaken for all special effects activities, and controls implemented;
- ensure that emergency and first aid procedures are followed;
- ensure personal protective equipment specific for special effects work is provided to, and used by, workers when required;
- ensure workers know escape routes, when working around or near special effects, before entering the work area.
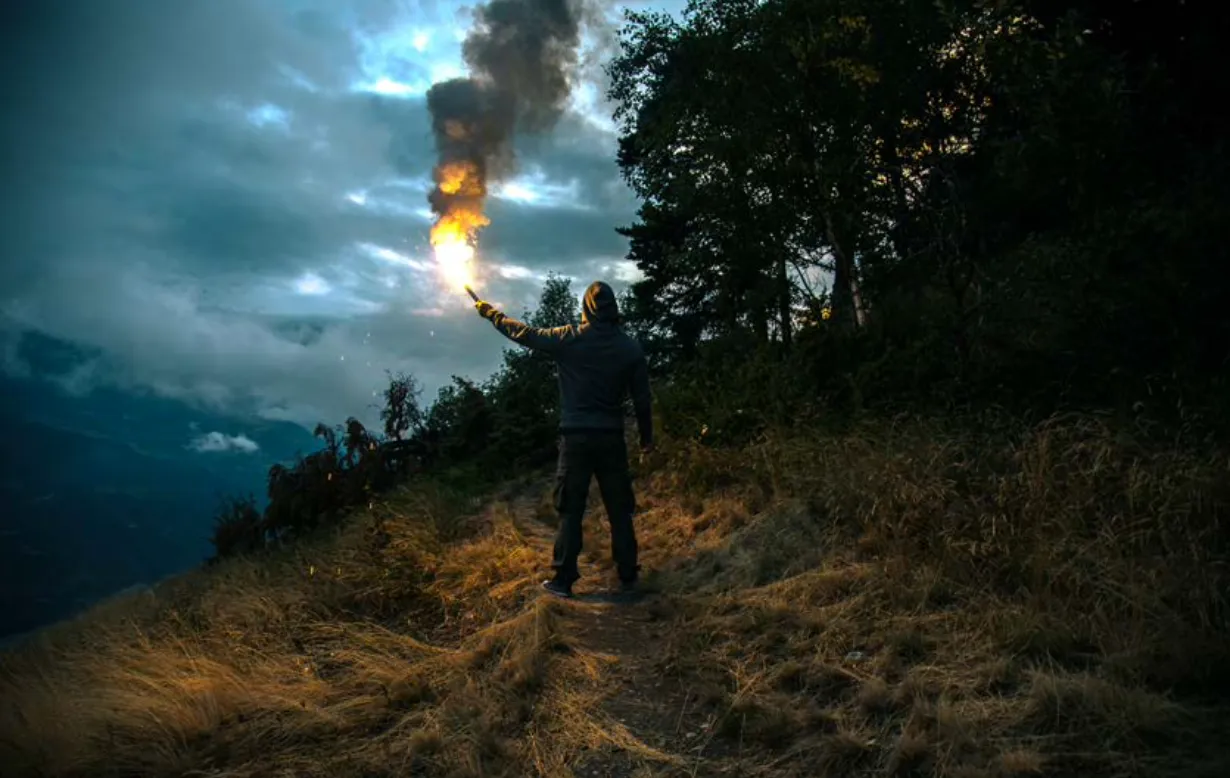
Special Effects Supervisor
The SPFX Supervisor should:
- ensure all SPFX Technicians have the necessary skills, certifications and experience to ensure safe and compliant outcomes for the production;
- carry out adequate testing of all special effects during pre-production and, where possible, ensure that such testing is carried out in the presence of all relevant heads of department and those cast members involved;
- set exclusions zones based on testing data to contain risk to cast and crew;
- always have in their possession all necessary permits and licences covering products and equipment used to carry out their contract of employment, together with literature on all relevant chemical compositions and safety guidelines regarding the use of pyrotechnics and flammable materials;
- ensure notification is made to the appropriate authorities, as outlined in the Health and Safety at Work (Hazardous Substances) Regulations, of the planned use of explosives and pyrotechnics or open flames;
- prepare an emergency response plan, which includes acceptable avenues of escape;
- ensure they, and all SPFX Technicians, have a suitable approved handler certification for any pyrotechnic work undertaken;
- organise a walk-through and safety brief before any hazardous sequence;
- consider how changing deadlines and making set changes at the last minute can lead to fatigue and stress for workers; and
- if there are problems relating to special effects on set, find practical solutions that don’t affect health and safety and, if necessary, raise concerns with the production to ensure safety.
Health and Safety Officer
The Health and Safety Officer should:
- work with the SPFX Supervisor to identify all potential risks;
- liaise with the appropriate competent persons to identity and implement appropriate controls for all risks;
- ensure workers are provided, or advised of, the appropriate personal protective equipment required on the location; and
- ensure workers know escape routes, when working around or near special effects, before entering the work area.
Responsibilities specific to Special Effects
General safety procedures
Competent Person
Only a competent person, such as a SPFX Supervisor or SPFX Technician, may carry out mechanical or pyrotechnic special effects.
A suitable approved handler certification is required for any pyrotechnic work.
Fatigue
Changing deadlines and set changes at the last minute can lead to fatigue [add link] and stress for workers; such impacts must be taken into consideration and minimised.
Notification of Planned Use
Notification to the appropriate authorities, such as WorkSafe and / or closest Police or Fire and Emergency communication centres, of the planned use of explosives and pyrotechnics or open flames must be made as required in the relevant Regulations or local bylaws.
Notification to Personnel
All personnel must be notified that explosives and pyrotechnics, open flame/fire sequences or smoke producing equipment will be used and briefed on safety precautions.
Emergency Response Plan
An emergency response plan must be prepared, including acceptable avenues of escape.
Permits and Licenses
The relevant permits/licenses must be held by those using and supervising special effects.
Safety Briefing and Walkthrough
Before any potentially hazardous sequence is performed, an on-site meeting should be called for all personnel who are involved in, or working near, the sequence. The meeting should include an "on-site walk-through" or "dry run" with the SPFX supervisor and all personnel directly involved in the event.
The SPFX Supervisor should clearly identify:
- the intended action
- possible deviations;
- communication signals and chain of command;
- authority to abort event;
- acceptable avenues of escape;
- location of necessary safety equipment and personnel.
Substantial Changes to the Planned Special Effect
If at any time substantial changes become necessary, another meeting should be called to confirm everyone's understanding of, and agreement to, the change(s).
Live Rehearsal
A live rehearsal should be held whenever practicable.
Emergency Vehicle Access
There must be a clear access for emergency and firefighting equipment and vehicles.
Effect of Special Effects on Studios/buildings
When planning the use of special effects in a studio/building, expert advice, such as that from an engineer or test certifier, should be sought as to how such effects might affect or be affected by the studio/building itself.
Firefighting Equipment
Appropriate and sufficient firefighting equipment must be provided and available immediately available on set.
Smoking
A ban on smoking and naked flames must be enforced in the entire area in which the special effects is being created, including workshops and storage areas.
Explosives and Pyrotechnics
Anyone using explosives or pyrotechnics should also read and understand the chapter on hazardous substances.
Restrictions on Use
The use of explosives and pyrotechnics are set out under the Health and Safety at Work (Hazardous Substances) Regulations 2017.
WorkSafe New Zealand enforces the statutory regulations on the use of, transportation, importation, storage and of explosives and pyrotechnics.
Any use of explosives or pyrotechnics for filming must be under the control of someone who has a “certified handler” certification for the classes of pyrotechnics being used in addition to a “controlled substances licence” listing the classes of pyrotechnics for explosives being used.
SPFX supervisors conducting pyrotechnic sequences that fall into the category of a fireworks display, must ensure they obtain an "OPD (Outdoor pyrotechnic display compliance certificate)".
The Discharge Area and Exclusion Zones
The Health and Safety at Work (Hazardous Substances) Regulations 2017 set out the requirements for discharge area and exclusion zones.
The discharge area is where the pyrotechnic effect is initiated. The exclusion zone6 is the area where the hazardous effects of the
discharge are contained.
The SPFX supervisor or certified handler in charge of the detonation or deflagration should determine the exclusion zone to ensure no person is exposed to adverse:
- heat radiation;
- blast overpressure; or
- fragmentation.
Exclusion zones are best determined through testing.
Testing must be scheduled away from the day’s shooting and prior to filming the effect and is required to determine safe distances and minimum quantities of explosive necessary to produce the effect.
Where objects are projected into the air, the testing method must be with the objects themselves or their equivalent to ensure the effect and the outcome is correctly simulated. Any subsequent changes made to the effect after initial testing will require a re-run of the testing procedure.
Restricted Access to the Exclusion Zone
The certified handler in charge must have complete control over who enters the exclusion zone; only crew and cast members necessary for filming should be in the exclusion zone.
After each pyrotechnic event, no one should enter the pyrotechnic area other than the pyrotechnic special effects operator in charge, or their designated representative(s), until it is declared safe. This includes for testing, rehearsals and filming.
Detonation of Pyrotechnics or Explosives
A sequence of firing cues and a strict routine of rehearsals should be established and understood by all involved.
Pyrotechnic special effects should not be fired unless the area involved with the firing is in the continuously unobstructed full view of the pyrotechnic special effects operator in charge, or their designated representative, at the time of firing, unless equal means of observation are used.
Appropriate fire watch, as determined by the certified handler in charge, should be maintained after each pyrotechnic event.
Reducing Risk of Unintended Initiation or Detonation
Radio transmissions of any kind, including mobile phones, should be turned off in the explosives area, unless exempted by the SPFX supervisor. This restriction applies from the start of the preparation of pyrotechnics until after the explosives area has been cleared by the SPFX supervisor.
In the event of audible thunder or visual sighting of lightning, all pyrotechnic or explosive work must be suspended and made safe.
There must be no smoking or any type of fire, spark or other source of ignition near any explosives.
To protect against accidental firing, all electrically fired pyrotechnic devices should be shunted prior to firing.
Power sources for firing pyrotechnic special effects devices should be restricted to isolated ungrounded batteries or individually designated ungrounded generators (below 5 kilowatts to comply with non-grounding requirements) used exclusively for firing purposes only.
Bullet Hits and Rigging Body Bullet Hits
Only use custom-made bullet hits designed for use in the close vicinity of crew and cast members.
Only the SPFX sSupervisor or SPFX Technicians should rig body hits.
All body bullet hits should be tested prior to use with the same fabric or costume.
The rigging of any type of pyrotechnic device to a performer needs to be done by a SPFX Technician and have been sufficiently tested.
Open flames
Restriction use of LPG
LPG is a Class 2.1.1A hazardous substance, and its use is governed by the Health and Safety at Work (Hazardous Substances) Regulations 2017.
If there is more than 100kg of LGP on set, it must be under the direct control of a certified handler or secured correctly.
A non-approved handler may handle the product provided a certified handler is present at the location and available to assist or has provided guidance to the use and handling.
Once the quantity of LPG in a location is over 100kg this activates the requirement to establish a Hazardous Substance Location and a Hazardous Atmosphere Zone.
Flammables and Combustibles
Flammable and combustible materials need to be kept a safe distance from open flames and in approved labelled containers.
When used on set to act as a fire accelerant, continual ventilation needs to be initiated until ignition or clean-up and storage is completed.
When LPG is used to provide a yellow flame, carbon monoxide is produced, so adequate ventilation needs to be maintained.
Each LPG tank "shut-off” location should have an operator who always has a clear view of any LPG fires.
All gas lines in connection with the use of open flames need to be rated and appropriate for use with gas/LPG.
All stationary open flame fixtures and devices need to be firmly secured.
The fuel source for special effects fire rigs need to be sufficiently isolated/bunkered/ distanced from the remainder of the crew to avoid any risk to personnel in the event of a flashback. The use of flash back arresters is advised.
On an interior set where smoke and open flame are used together, precautions must be taken to ensure the smoke does not reach a level of density where it could ignite from the open flame.
Fire Area
The producer or person with delegated responsibility and the SPFX supervisor should determine the fire area. Only essential personnel should enter the fire area.
Fire and Provision of Respirators and Personal Protective Equipment
When creating a fire, the operator should exercise all reasonable precautions to prevent heat and smoke inhalation and should make respirators available on request ¬– respirators should be appropriate for the type of smoke.
Cast and crew near open flame should wear appropriate protective clothing. Depending on the hazards involved, this clothing should include appropriate closed-toe footwear, long pants and a long-sleeved shirt made of 100 percent cotton or material which provides equal or greater protection.
Cast and crew need to be notified by the designated responsible person when there is potential for exposure to open flame. Appropriate personal protective equipment must be for the hazard(s) involved and considerations must be made for head, hands, eyes, ears and respiratory protection.
Atmospheric effects
Artificial Smoke and Mists
Bronchial sufferers
Cast and crew should be warned of the risk caused by artificial smoke and mists, and effects, to sufferers of bronchial disorders. Bronchial sufferers need to be provided with appropriate respiratory equipment if required to be in the vicinity the effect.
Type of chemical
The type of chemical selected should cause the least respiratory irritation and be safe to use.
Dense artificial smoke can be highly flammable. Special care should be taken to prevent ignition from any source. An MSDS for each substance used should be immediately at hand.
Exposure to artificial smoke and mists
Exposure to artificial smoke and mists should be kept to a minimum. When smoke or fog effects are created on an interior set, the stage needs to be periodically ventilated or exhausted, vertically and laterally. All personnel and animals should be given a break away from the stage at appropriate intervals.
Ventilation
When using smoke on an interior set on location, the creator(s) needs to provide a means to exhaust or ventilate the set.
When smoke and/or mist is created on an interior set, the stage needs to be periodically ventilated or exhausted, vertically or laterally. All people and animals should be given a break away from the stage at appropriate intervals.
Provision of protective respiratory equipment
The producer or person with delegated responsibility needs to provide specialised respiratory equipment when personnel are exposed to long or intense periods of artificial smoke or mist.
Evacuation of crew and cast rooms
When artificial smoke and/or mist is used on any interior set, all non-essential personnel should be removed from all areas close enough to be affected by the smoke or mist.
Water Effects
All water used in rain sequences where the water falls on cast and/or crew should not pose a health risk.
Only appropriately licensed and authorised personnel can draw water from hydrants and stand pipes.
All personnel operating nozzles must be adequately trained in their use.
Fire hoses must be routed to minimise danger (of electrocution or whiplash from the fire hose) if a coupling failure occurs.
Hoses must be maintained in sound working order to avoid rupture.
Ramps must be used to cover hoses whenever there is pedestrian or vehicular traffic.
Rain stands and sprinklers must be adequately sandbagged and secured to prevent them from toppling over.
Electrical Safety in Conjunction With Rain and Water Effects
AS/NZS 4249: Electrical safety practices—Film, video and television sites and all relevant regulations must be complied with during rain and wet-down effects.
All electrical cables must be insulated and must be kept off the ground wherever possible to avoid electrical current being carried through the water.
All single phase and three phase outlets, leads and three-pin connections must be kept dry. Where possible, submersible cables should be used.
Snow Effects
When snow effects are being carried out, materials used must have an MSDS and be used in accordance with relevant technical information.
Mechanical Effects
Breakaways
When constructing breakaways, a competent person, SPFX supervisor or SPFX technician should be consulted.
Hydraulic and Pneumatic Ram and Gimbal Systems
Hydraulic or pneumatic jerk rams, deadweight drops, shaker motors and any mechanical rigs need to be used according to manufacturer recommendations, and risk assessed and documented on a rig-by-rig basis, including:
- establishing an exclusion zone around the rig that ensures no cast or crew are struck or injured by the moving parts or any projectiles coming from it;
- ensuring only SPFX technicians trained in the safe use of the equipment are in control of its operations; and
- ensuring the rig and safety procedure have been extensively tested before use around cast and crew.
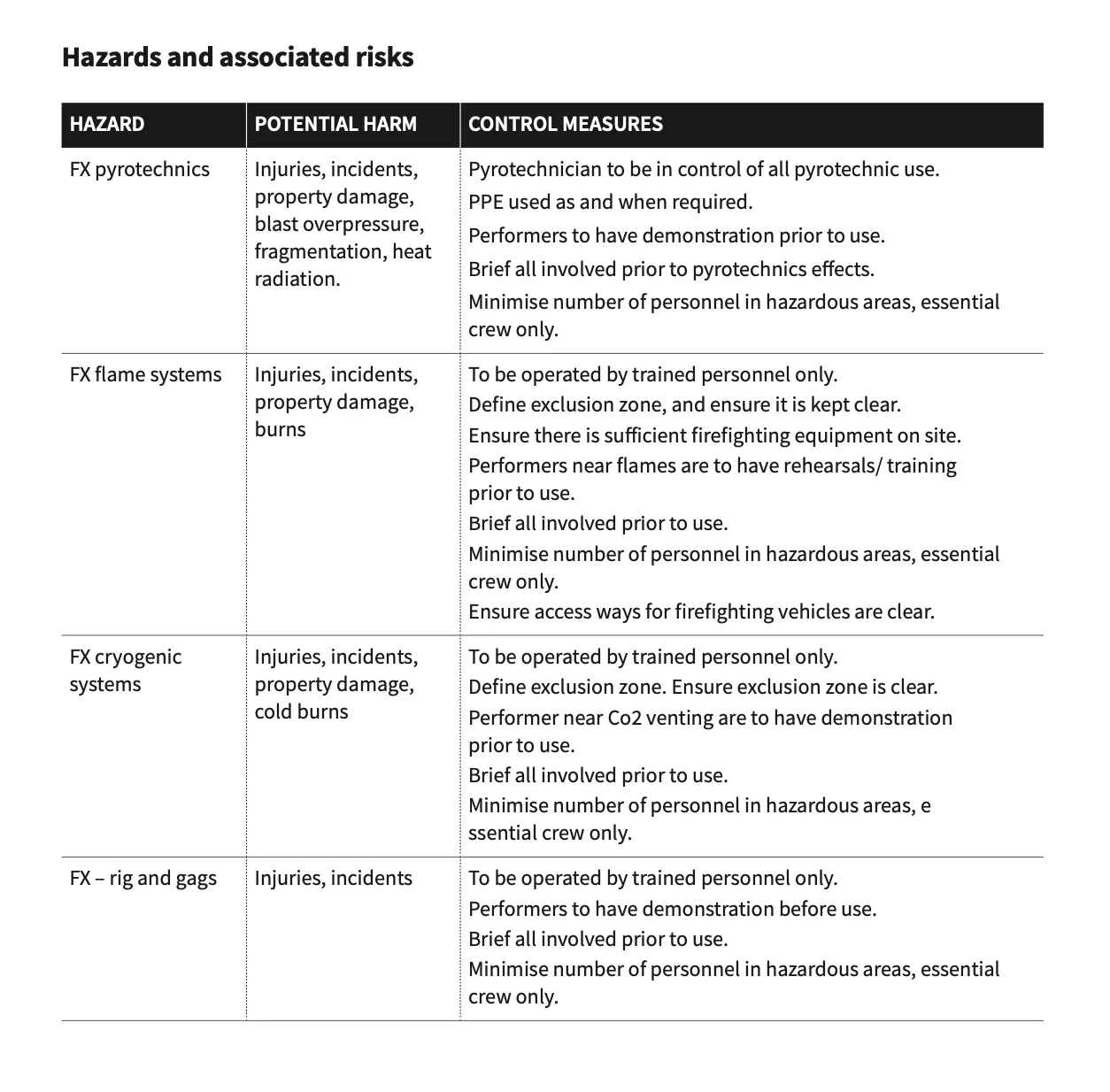
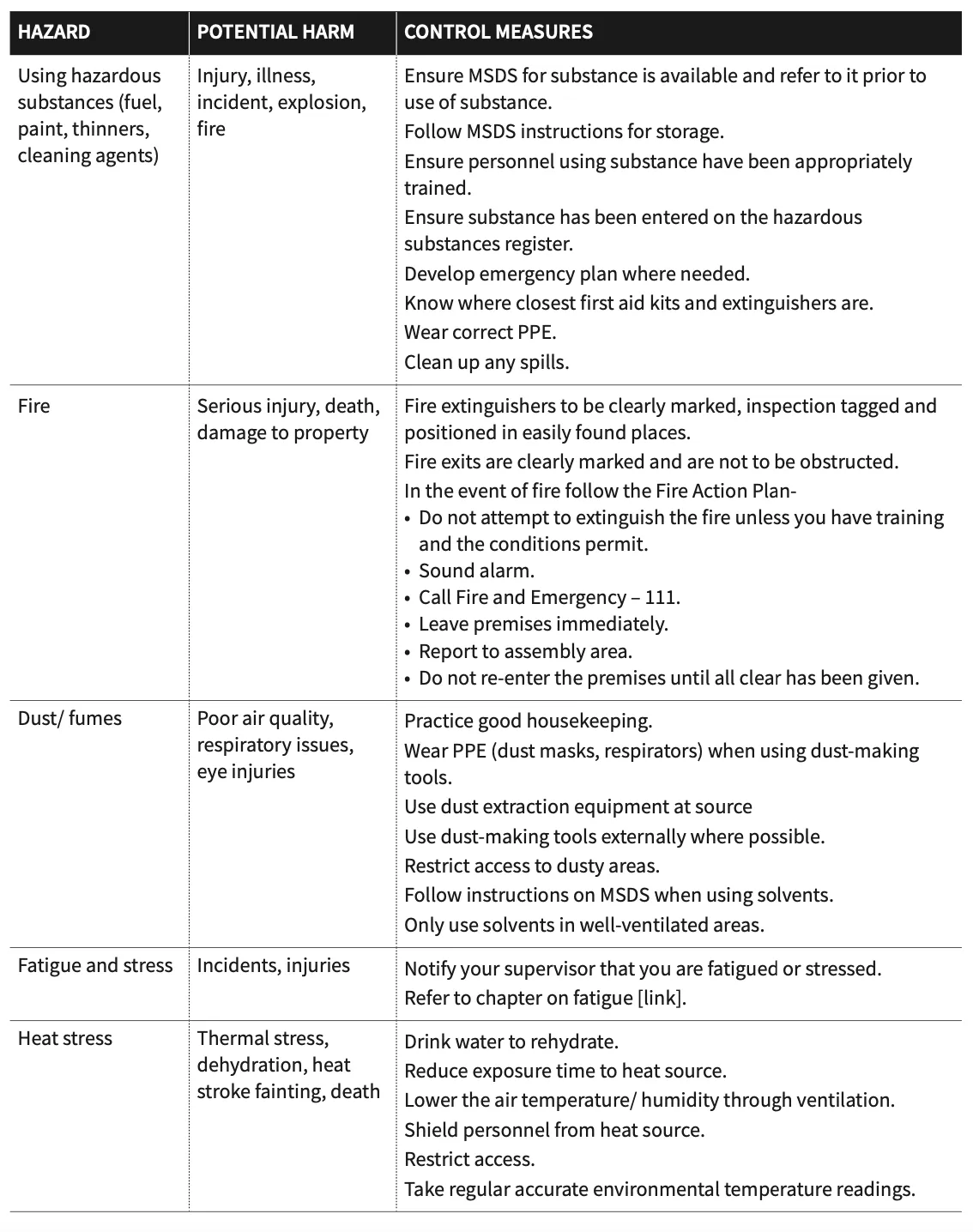
Training
Anyone handling or working with hazardous substances must have the appropriate training and knowledge as outlined in the hazardous substance chapter.
SPFX Supervisors and Technicians taking a lead role in pyrotechnics should be a certified handler and have a controlled substance license for any class 1 substances being used.
A handler certification should be held for Class 2 and 3 where quantities of those exceed the thresholds listed in Table 2 of Schedule 9 Health and Safety at Work (Hazardous Substances) Regulations 2017
References
Health and Safety at Work (Hazardous Substances) Regulations 2017